Why Dehumidify?
Before discussing the details of dehumidification, it is important to understand why it is important to control humidity within a greenhouse at all.
When humidity is low, evaporation rates increase which can cause water stress on the crop and will raise humidity regardless. Photosynthesis is optimised at a relatively high humidity level, as it promotes stomata opening, however, when humidity gets too high then photosynthesis is stifled and disease risk increases.
Significant energy savings are available when accepting a higher maximum humidity level, but this can increase risk unless the horizontal and vertical temperature gradients are very low, and sufficient air movement fans are employed.
Regardless, active plants are recruiting water through the roots and therefore must expel water through their leaves to facilitate this. Eventually, this water must be removed from the growing environment. Some water is removed via condensation on the glass surfaces, but the bulk is typically removed via ventilation.
Heating Pipe & Ventilation
Ventilation reduces humidity based on the principle that ambient air often has a lower absolute humidity (AH) than internal air. The figure below graphs the relative humidity (RH) at 18°C against saturated air at various temperatures. This illustrates how RH changes at different temperatures with a static AH.
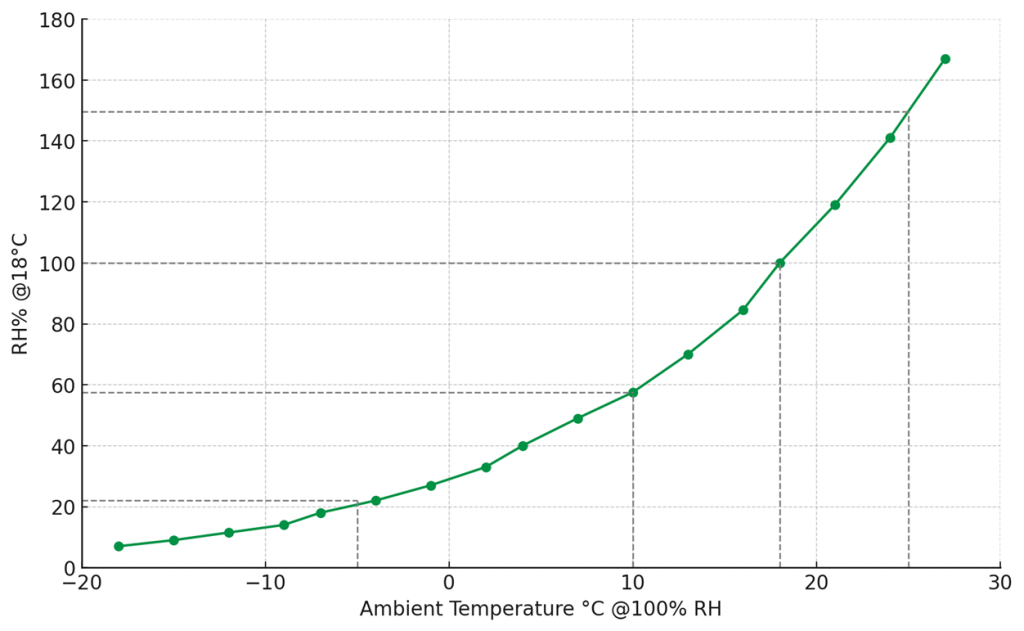
A few intersects have been added; saturated air (100% RH) at -5°C reduces to around 20% RH when brought up to 18°C, -10°C reduces to 60% RH, and 25°C increases to around 145% RH when cooled to 18°C.
This shows that even when ambient humidity is high, water can be removed from a greenhouse, given there is a sufficient temperature difference between the internal and external temperatures. Ventilation struggles to reduce humidity when ambient and internal temperatures and humidity are similar, e.g., warm and wet summer days/nights.
Psychometrics is a complex field and understanding the energy needed to remove water from a greenhouse through heat pipes and ventilation is not straightforward. To simplify figures, the table below outlines three scenarios, where humidity is reduced from 80% to 70% RH through ventilation with pipe heating, at varying ambient temperature.
Starting Humidity (RH) | 80% | ||
Ending Humidity (RH) | 70% | ||
Internal Temp (°C) | 18 | ||
Ambient Temp (°C) | 5 | 10 | 15 |
Energy Requirement (kWh/l) | 2.78 | 1.71 | 0.64 |
It is important to note that these figures ignore the humidity levels of the incoming air, they represent only the energy required to remove a volume of air containing 1 litre of water from the greenhouse, and heat the replacement volume of incoming air up to 18°C.
The energy requirement above is sensible heat only, needed to raise the temperature of the incoming air. In a greenhouse environment, latent heat of around 0.68kWh/L is also needed to evaporate liquid water within the greenhouse.
Assuming an internal and external CO2 ppm of 800 and 400 respectively, removing 1L of water in this way also removes approximately 300g of CO2.
Although vent angle can be adjusted, opening vents and using heating pipes is inherently hard to fine tune. Ambient and internal temperature and humidity, as well as wind speed all factor in to vent opening angle. However, pipe warm-up, cool-down, and heat distribution time (i.e., how long it takes for an increased pipe temperature to be felt within the surrounding air) all work to reduce how efficiently a change in humidity will be enacted. In addition, the action of opening vents can only be as precise as the sensors feeding into the control system.
The figures outlined above are ideal scenarios, assuming that the structure ventilates only the exact volume of air needed to remove 1L of water. In practice, the air volume and therefore energy cost figures are likely to be much higher.
Mechanical Ventilation
Mechanical ventilation can ensure that the volume of air removed to reduce humidity is more optimised. One of the manufacturers with this type of unit is Van Dijk Heating, who have gable-end wall units connected to long ventilator ducts to distribute the incoming air at floor level.
In principle, the energy requirement for mechanical ventilation will be equal to the table above for ventilation; although, controlling air transfer through a mechanical ventilator allows for more precise intervention and should lead to energy savings by itself. However, by including a heat exchanger in the ventilator, warm outgoing air can pre-heat the incoming air, reducing the need for additional heating. Van Dijk suggest that savings of around 40% are available, compared to typical ventilation.
Similarly to an HVAC unit, controlling air flow in this way allows for additional heating/cooling of the incoming air to match the crop needs. Additionally, these units use forced air movement which leads to improvements in temperature and humidity distribution throughout the growing environment, discussed in more detail in our previous article, Air Movement & Humidity.
Dehumidifiers
One way to remove humidity from the air, whilst retaining heat and CO2, is by using internal dehumidifier units.
These types of units typically make use of a refrigerant cycle: compressing and expanding refrigerant fluid to transfer heat from a cool environment to a warmer environment. Reducing the temperature of air reduces its saturation point, meaning that at a stable AH, the RH will increase. When RH increases enough, some of the water condenses out.
Rather than venting heat from the refrigerant cycle, which is how typical refrigeration systems operate, dehumidifiers can use the reject heat to reheat the cooled dried air. Heating dry air requires less energy than heating wet air, and refrigeration cycles are very efficient, which leads to energy savings. Warm dry air is then circulated back into the crop using fans.
One of the common internal dehumidifier manufacturers is DryGair. Each of their standard units can extract 45L/hour at the cost of 10kW of electricity. This leads to an energy requirement of 0.22kWh/L, between 65-92% less energy than the heating pipe with ventilation figures above. In practice, given the ranges in ambient temperatures and humidities, DryGair advertise an average of 50% saving.
In addition, these units maintain CO2 levels within the glasshouse, meaning even less natural gas combustion. Again, these units promote air movement with the recirculation fans, which has several benefits for humidity and temperature control.
Alternatives
Aside from the methods discussed so far, there are alternative methods of dehumidification, namely, direct condensation on a cold surface and hygroscopic materials.
Cold plate condensation is simple in principle, and the heat removed from the system can be captured and recirculated into the glasshouse. However, the ratio of sensible to latent heat removed from the growing space (i.e., how much the plate cools the space compared to how much water is condensed) is high, meaning that the cooling system becomes inefficient and expensive to operate for to how much water is removed.
Hygroscopic materials are concentrated salt solutions which absorb water and latent heat from the air, which can be recovered into sensible heat. However, the materials themselves have environmental risks and their replacement is expensive. For this reason, it is unlikely these will be suitable for use in a greenhouse.
Written by Eirinn Rusbridge