Growing many horticultural crops is necessarily energy intensive, particularly when targeting important out-of-season markets. Energy has always been an important consideration for these businesses, but the past few years have increased costs by double or more, making the management of energy one of the foremost concerns in protected horticulture.
What is an energy audit and why does it matter?
At its simplest, an energy audit is a site survey focusing on energy use. The purpose of this is to better understand how a site uses energy, highlight opportunities to reduce or optimise energy use, and quantify the energy and monetary savings to help prioritise projects.
How do you carry out an effective energy audit?
The outcomes of an audit can only be as detailed as the inputs; as data gets more granular, more information can be extracted from it. For example, half-hourly electricity import can give insights into daily trends of when a site uses electricity and identify when unnecessary power is being used. Likewise, monitoring fuel use by individual vehicle allows you to target technology improvements or driver training.
Keeping a good record of all energy use on site and performing comparative analysis on these data is key. Submetering, fuel cards, and more sensors feeding into a sophisticated management system can all contribute to this.
A site walkthrough is then essential to give more context to the available energy use data. The power rating and typical run hours for energy using equipment is recorded, setpoints and management systems are scrutinised, and questions are posed as to site-specific processes. This all allows an auditor to pose relevant energy, cost, and carbon savings measures.
Ultimately, savings measures fall into one of two approaches: reduce the load, or reduce the run hours, required to perform necessary tasks. In practise, many measures will do both. Here are some examples:
- Reduce load;
- Adjust setpoints,
- Upgrade old/inefficient equipment,
- Improve insulation,
- Optimise processes,
- Reduce time;
- Adjust setpoints,
- Install timers or occupation sensors,
- Improve metering/sensors,
- Training & behaviour changes.
Finally, once improvements have been made, keeping on top of data collection and analysis can ensure that the changes have been effective. Tracking performance will indicate whether a new system is working correctly and detect faults early, and benchmarking against your production will help to quantify paybacks.
Energy saving opportunities: some examples
Adjusting setpoints
One way to quantify the potential savings from running a heating/cooling system is by performing a degree day analysis. Heating degree days (HDD) are a measure of how often, and by how much, ambient temperatures are below a setpoint. They therefore indicate how hard a heating system must run to meet a setpoint. The following table shows an HDD difference for typical setpoints at a site in the South of the UK.
Setpoint | HDD | Saving |
18° | 2,909 | – |
17° | 2,579 | 11% |
16° | 2,264 | 22% |
For this site, a 2° temperature setpoint drop leads to a 22% reduction in HDD. This does not translate directly into reduced heating system load, but it is a good high-level estimate.
Upgrading lights
LED fixtures typically require less power to deliver the same illumination as other lighting types. Replacing fixtures must be done carefully, to ensure that light coverage is consistent, but a 30% saving should be available over most conventional bulbs. The following table quantifies this.
Lighting | Hours | MWh/year | MWh Saved |
1,000kW HPS | 2,000 | 2,000 | – |
700kW LED | 2,000 | 1,400 | 30% |
LEDs also allow for faster response to controls and can have adjustable spectra, which can increase how much the light drives photosynthesis in the crop and potentially improve yields.
Installing and replacing screens
Energy screens can provide a huge potential saving where none are currently in place. Additionally, replacing aged and broken screens can make financial sense. The following table shows how much some different screen types can save energy, in comparison to no screening.
Screening | Saving |
Shade | 20-25% |
Clear/diffuse | 47% |
Thermal | 50-70% |
Blackout | 70% |
Employing a combination of screen types can give significant savings over no screening at all. Double and even triple screens are possible, which can minimise thermal losses to an even greater extent, whilst effectively managing light and humidity.
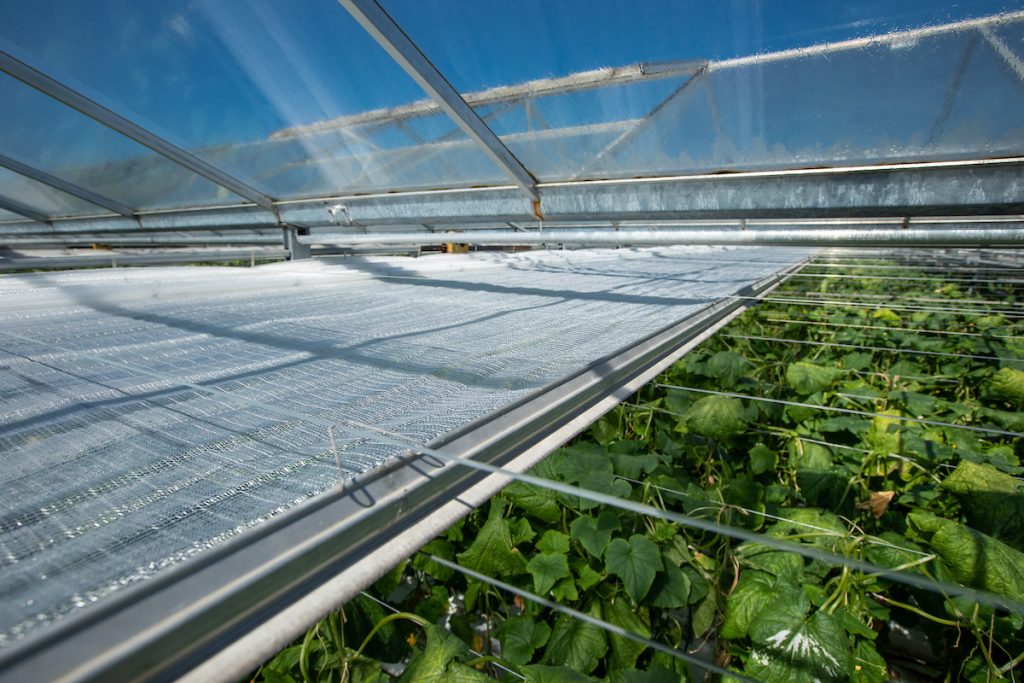
Written by Eirinn Rusbridge
To find out more about conducting an energy audit on your site, feel free to get in touch with NFU Energy.