Screens are an important element of glasshouse production as they have a key role in how you control the growing environment. Learn how you can use them effectively to help optimise greenhouse energy efficiency.
Although adding screens to glasshouses is common practice across protected horticulture., there is often a general attitude of ‘set and forget’ with regards to screening, whilst developers and manufacturers make consistent improvements in cloth performance. This has lead to a large number of screening systems that are need updating or are not performing at their optimum.
There is a historic notion that screens should have a lifetime of around 15 years, but warm and humid growing environments as well as frequent opening and closing can lead to much shorter lifespans. Algae growth and general wear and tear can reduce the lifespan to as little as 5 years; and a soiled screen will have significantly reduced light transmission, and holes and tears in the fabric will cause a much reduced thermal performance. Therefore, it is important to monitor the condition of existing screens to determine whether it is time to replace.
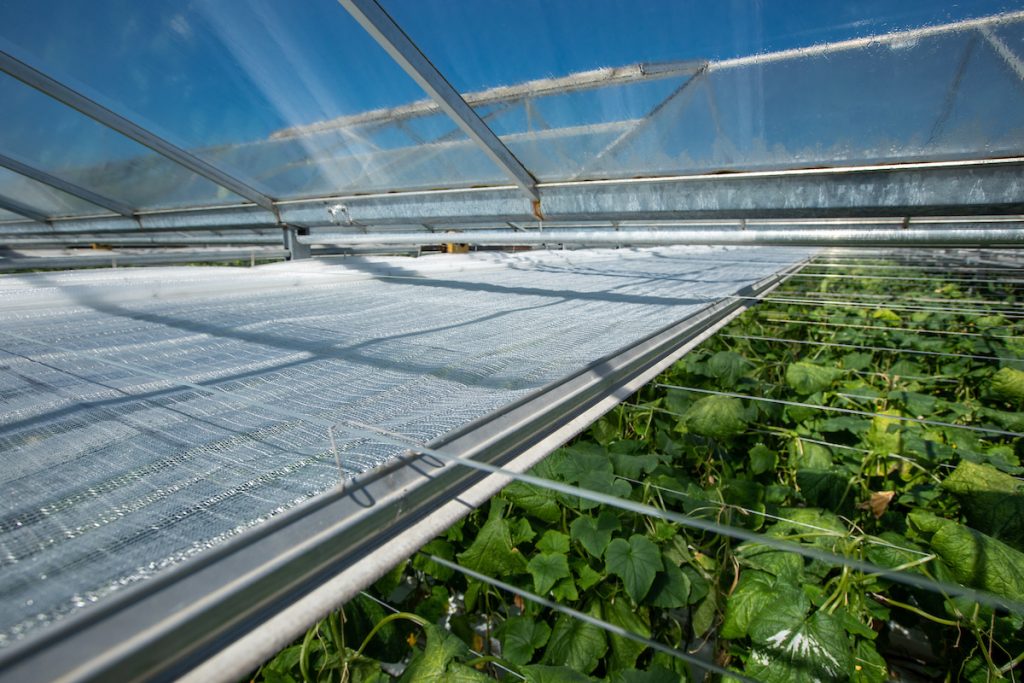
Why install screens?
Screens are installed for one or more of three reasons:
- reducing heat loss
- providing shading
- mitigating light pollution.
Different materials exist which are specialised to perform each of these tasks, and combining screens in double or triple configurations allows for versatility in strategy.
The greatest recent innovation in screen fabric has been their light transmission. Screens such as Svensson’s Luxos range are capable of shading levels between 19-25% and 11-15% in diffused and direct light, respectively, while maintaining energy savings as high as 47% (compared to no screens). High transmission screens like these can also diffuse light passing through them. Read more about the benefits of diffuse light here.
Shading screens are cheap, widely available, and provide good shading and humidity control, but only save between 20-25% energy over having no screen. Newer thermal shade screens have strips of higher-performance material alongside higher light transmission material. Depending on the configuration of the strips, between 50-70% thermal savings are available. Blackout screens are then the best thermal and shading screens available, with up to 75% thermal savings. These can have white, black, or reflective layers, which can cool down the glasshouse by reducing solar gain or ensure that supplemental lighting is reflected back down onto the crop.
Side screening can be very beneficial to smaller glasshouses, since their sides make up a large proportion of their total surface area. Bubble wrap is common because it is cheap and a good insulator. However, it is prone to moisture and therefore algae growth, which limits light transmission. As well, bubble wrap is often left in-situ for long periods of time. Vertical screening has similar thermal properties but can be retracted to allow the crop to benefit from direct light and solar gain.
For a large growing area, a single screen with drive wire will cost in the region of £11-13/m2. This cost is influenced strongly by economies of scale, meaning small areas can be as expensive as £40/m2. Modern cloths tend to be lightweight, but multiple screens should be driven by separate systems so that their versatility can be realised. This means that double screening will cost roughly twice as much as single screens.
Managing effective screen systems
Dutch growing techniques, such as Next Generation Growing, suggest that rather than gapping screens, breathable cloths can be left closed whilst venting above. This maintains the energy saving ability of the screen, while allowing for humidity control. Paired with venting on both the lee and wind sides of the glass (minimum opening on each), air movement (and therefore water movement) will be maximised. If screens must be gapped, it should be limited to around 5% to maintain some of the thermal performance of the screen.
Glasshouses tend to be built on a slope. This means that cool air above the screen will pool towards the lower end. When the screen is gapped, the body of cool air will fall directly into crop, creating a pronounced cold spot and increasing localised condensation. Apex screens can limit this movement, but minimising gapping should be prioritised regardless.
More complex systems necessitate more complex operation, which must be facilitated by adequate sensors and management systems. Homogenous growing environments lead to a more uniform crop, and implementing more sensors is the only way to track and correct for this. Management systems such as Priva are already sophisticated enough to manage screening strategy, but they should be enabled by an array of sensors both above and below the screens.
What does this look like in practice? A Case Study:
Studies at Wageningen university have shown that by employing a shading screen on a rose growing area, for shading and photoperiod manipulation, led to an increase in yields by up to 5%. As well, a joint study between Wageningen University’s Research Centre and Svensson employed a diffuse shading screen over anthurium and bromeliad, which resulted in a 25% increase in plant weight, a 6-week reduction in cropping cycle, and elimination of plant scorching. Diffuse shading screens have also been shown to reduce the plant temperatures by as much as 2-3OC, by spreading the solar gain more evenly through the glass.
Installing a second screen over high-energy crop has shown to reduce energy demand by an additional 15-20%, over the single screen. The following table outlines the results from a, 11-month Svensson study on the effect of screening a pepper glasshouse in Canada.
No Screens | Scenario 1 | Scenario 2 | Scenario 3 | |
Screen 1 | – | Energy Screen | Energy Screen | Blackout Screen |
Screen 2 | – | – | Diffuse Cloth | Energy Screen |
Vertical Screen | – | – | Blackout Screen | Blackout Screen |
Gas Use (m3) | 3,646,792 | 2,687,951 | 2,280,452 | 2,147,293 |
Energy saving | – | 26% | 37% | 41% |
This article was written by Eirinn Rusbridge.
With many thanks to David Summerfield from Bridge Greenhouses for his input.