First published 2016
A look at the role of the type of refrigerant, the size of refrigerant charge, cooling methods, and the condition of equipment such as evaporators and condensers in the efficient running of the cold store.
Most cold storage relies on refrigeration technology and, in particular, the use of fluorinated gas refrigerants (sometimes called F-Gases, CFCs or Freon) to turn electrical energy into cooling energy. The relationship between these is called the Coefficient of Performance (CoP), which is defined as the ratio of output power or energy to input power or energy. Generally, CoP values for cold store equipment in the UK should be around 3, i.e. a delivery of 3kWh cooling for each 1kWh of electricity used.
Efficiency of equipment can be compromised by the type of refrigerant, depleted refrigerant charge (caused by leaks in the system pipework), increased ambient air temperatures, dirty or iced up evaporators and condensers, and system settings.
One simple way to ensure your system runs efficiently is to make sure the air directed to cool the external condensers is as cold as possible. Roof-mounted condenser units were commonplace on the sites visited in Denmark and it was pleasing to see that most systems’ condensers were clean. To ensure that the warm air exiting the condenser sets does not return to the inlet, maintenance staff retrofit units with low cost wooden baffles. Increasing the temperature of the inlet air by 10°C can see system performance reduce by 25% in worst cases.
A move towards Glycol filled units
With the legislation requiring an ever smaller refrigerant charge, there is a move, in both the UK and Denmark, towards Glycol filled units; an example of which was seen at a site run by Danplanex.
These Glycol systems still require a refrigerant filled compressor, condenser and evaporator to generate the cooling, but these types of system have all the components closely mounted. This is advantageous because there is less refrigerant in the system, shorter pipework means there are fewer opportunities for leaks, there is less potential for components to be damaged, and maintenance costs are reduced.
The evaporator is a plate heat exchanger, which transfers the cooling to a Glycol circuit, from where it is distributed to the stores at lower pressure. The evaporators in the store effectively become Glycol supplied fan coils; as the Glycol mix is significantly less cool than a refrigerant would be at this point, this type of store will need more fan coil units to deliver an equivalent quantity of cooling. Most stores seen had roof mounted cassette units. In similarly sized stores, those operating on Glycol had up to five times as many of these units.
One big advantage of using Glycol in the system is that heat can be recovered for use more easily. Danplanex were using the heat available to keep the offices warm, which reduces the electricity consumption of the refrigeration plant and also reduces the heating cost.
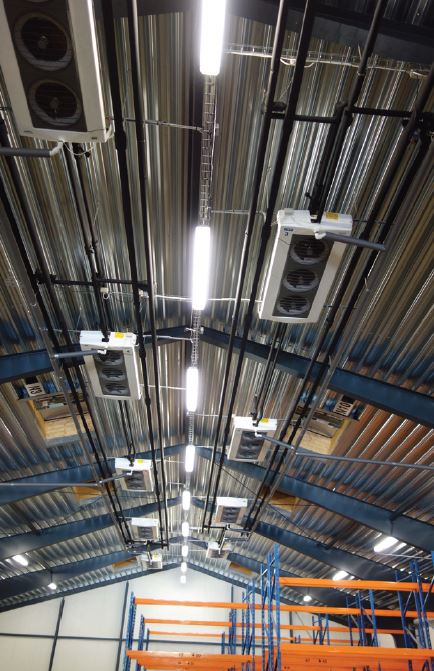
Water and ambient cooling
Another way of improving efficiency over a season is to use water to cool the refrigeration system rather than air. When cold stores operate during warmer spring and summer periods, the efficiency reduces as the ambient temperature rises. Water cooled refrigeration delivers 10°C cooling to the condenser unit year round.
This was investigated in AHDB Horticulture project CP 057, which found that up to 20% improvement in efficiency was possible.
Using ambient cooling is another way of improving the efficiency of your store. Ambient cooling can be delivered when conditions outside are colder than required; typically a temperature difference of 2°C or more will be beneficial. Ambient cooling can be as simple as leaving a door open on a cold night, but it is better done with fan assistance and using louvres that can be closed when not needed.
Back to: Cold store efficiency: What we can learn from Denmark