Via the GrowSave project, NFU Energy organised a 3-day Study Tour to the Netherlands in March for UK greenhouse growers. Our focus, of course, was energy – using it more efficiently, sustainably, cost-effectively and learning about new technology and innovation.
The Dutch are among the top commercial horticulturalist in the world, with a particular talent for greenhouse crop production. Managing energy is one the most challenging aspects of production, for which growers are always looking to find cost and efficiency improvements and solutions.
So, with about 20 UK soft fruit, cucumber, tomato and protected ornamental growers loaded onto a coach, we began our trip:
Solar for glasshouse heating
Our first visit was to Mol Freesia, a grower with a solar thermal glasshouse, where 1.5 hectares of field-mounted solar panels feed into a balanced system of heat pumps, storage tanks and bore holes to manage the heat requirements of their 4ha crop, producing around 18 million plants per year. The first of this scale in the Netherlands, they also combine the energy efficient growing principles of Next Generation Growing, and the use of LED lighting and water capture and recycling, for a growing model with optimal sustainability.
With investment into this model running well into the millions of Euros, Dutch Government incentive schemes have helped to make it possible. For more information get in touch with Certhon.
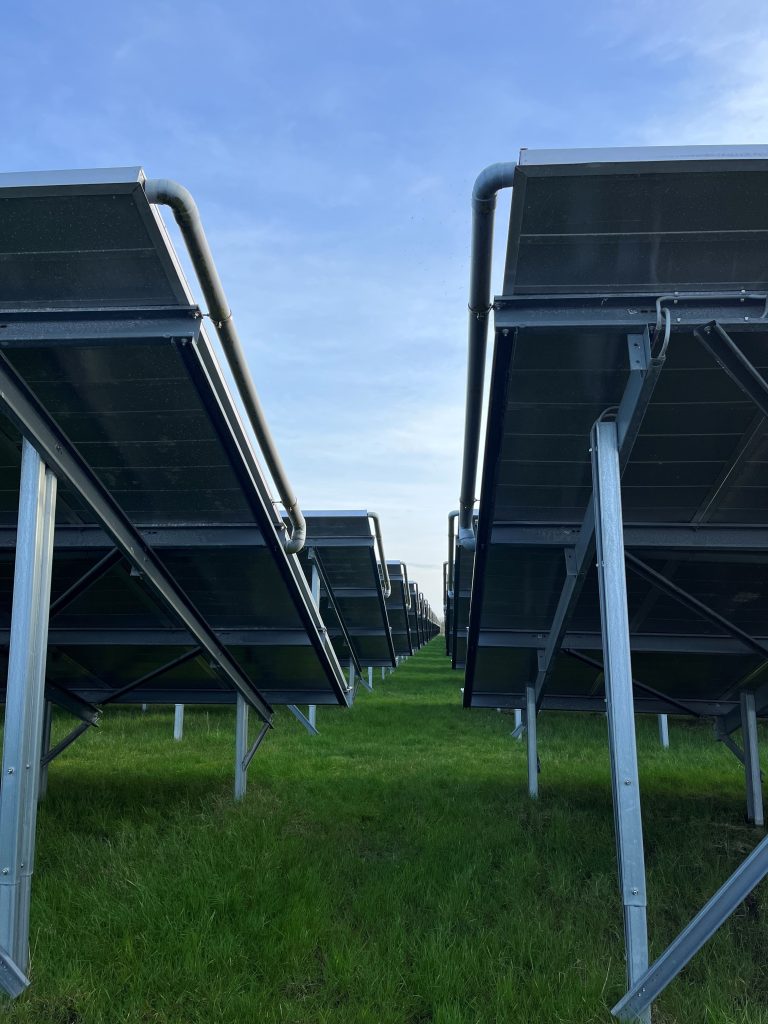
Capturing CO2 from biomass
Edible crops grown in greenhouses are commonly dosed with to CO2 to optimise plant growth and yield, but efficient, sustainable CO2 sourcing is a challenge. We visited DES, where 3 greenhouse growers joined forces to purchase a 7MW biomass boiler with combined CO2 capture providing year-round baseload heating and CO2 required for production of their 23ha of tomato and aubergine crops. The boiler is in constant operation and requires 50 tons of fuel per day with a 55-60% moisture level. With 2.2 tons of CO2 is produced per hour, and they are able to store 30 tons.
For a larger production area, this could be a promising set-up. Get in touch with Vyncke to learn more.
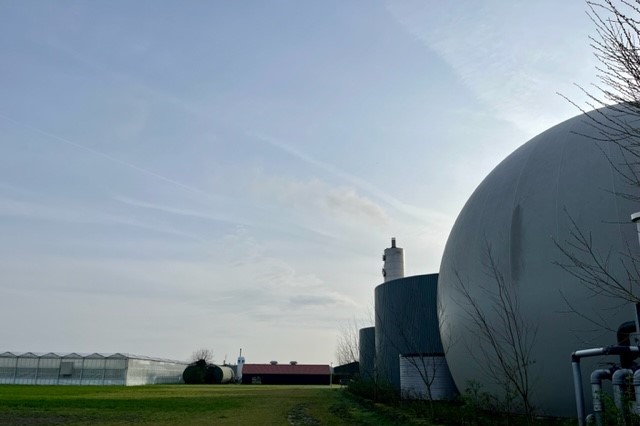
Recipes for lighting
Philips Horticulture LED, part of Signify, showed us around their GrowWise Centre, trialling and demonstrating optimal LED lighting for indoor crops. The campus on which it is located has been dubbed “the smartest place in the world”, with many different tech businesses as neighbours.
Their focus is to grow better plants faster, more reliably and sustainably, through tailored lighting recipes for individual grower priorities. Whether the desired output is growth speed, taste, or yield they will look to find the right recipe to balance these goals. Of course, there is always a trade off! A key development is a lighting recipe online program which can integrate with electricity spend to curtail lights during expensive hours.
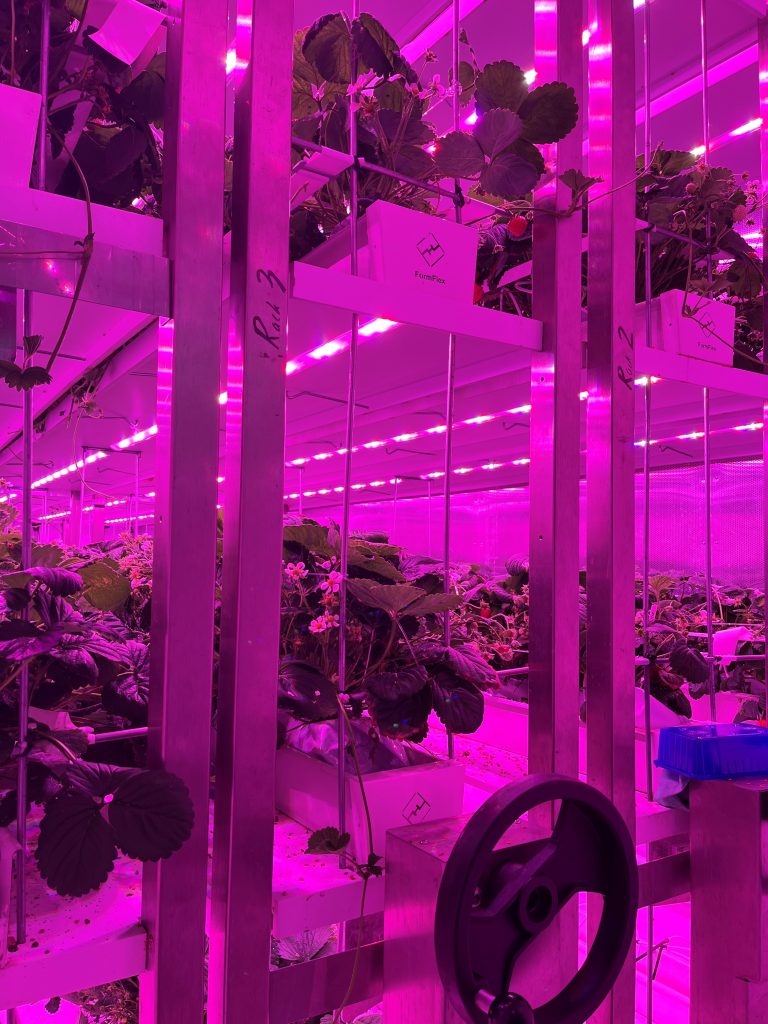
Energy efficiency trials
At Botany, a research centre which carries out novel greenhouse trials for growers, institutions, and private companies. We visited one which has the ambitious goal of achieving “energy efficient year-round tomato production with 40% less heat input”. Using a holistic approach combining dimmable energy-efficient LED lights, active dehumidification, double screens, and adapted nutrient management techniques they are tailoring all the aspects of cultivation for utmost efficiency with an acceptably reduced yield.
The active dehumidification is achieved with a ventilation unit installed at the gable end of the greenhouse, with heat recovery for dehumidification. Warm air is sucked in, heat is exchanged with ambient air and warm air is blown back through a tube along the length of the crop.
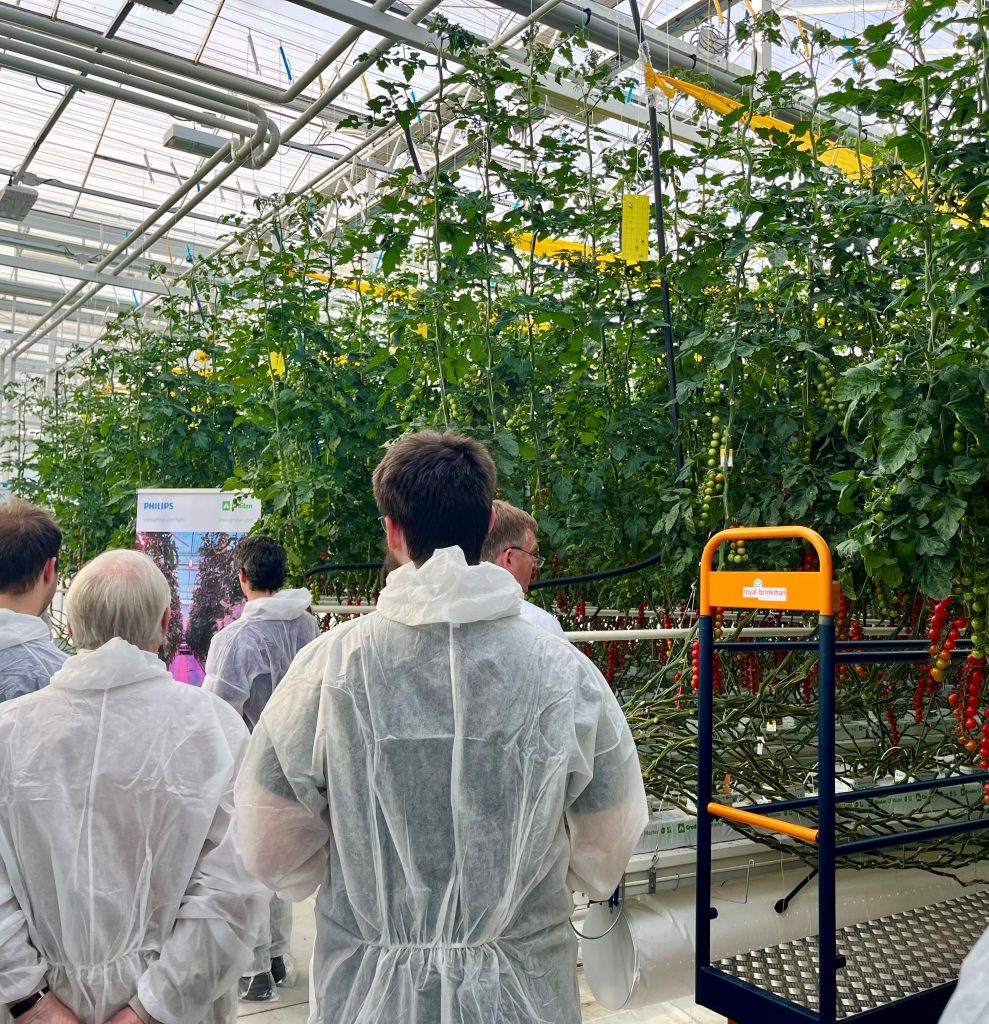
Air movement and dehumidification
Many growers and experts in the Netherlands advocate for the Next Generation Growing method, also referred to as Plant Empowerment, which focuses on enhancing plant health whilst reducing energy use and heat consumption. To improve plant health it is important to focus on the plant’s microclimate rather than the climate in the overall greenhouse structure, so it is key to have multiple sensors throughout the structure to properly monitor the environment. Additionally, an even climate is important to achieve a homogenous crop, so removing greenhouse leaks, reducing screen gapping and using apex screens are just some of the ways to help achieve this.
Some aspects of Next Generation Growing, including use of low-grade heat, improving insulation, and increasing screen hours, can lead to higher levels of humidity which can up the incidence of disease. Certhon, Svensson and Van Dijk presented their methods and new technologies for improving air movement and dehumidification to help solve this issue and regulate an even, balanced glasshouse environment. This included screen ventilators, such as the Climaflow, and gable ventilation units, such as the Active Ventilation System. Each system has its pros and cons, so it is important to prioritise your goals to help make the right decision for your greenhouse environment.
Novel materials and systems
Our final visit was to Bleiswijk, one of the experimental greenhouse sites run by Wageningen University, where they run trials on many aspects of greenhouse crop production from energy to robotics.
Of particular interest to our group was the trials on alternative greenhouse materials. Their “fossil-free” glasshouse trials different ornamental and edible crops with “low-E” coated glass – which claims a 15-20% saving on heat. Another trial looked at the growth efficiency of strawberry crops under F-Clean ETFE greenhouse panels, which allow a higher transmission of diffuse light into the greenhouse, for a full spectrum of light to reach across the growing area. These materials were being tested for their light and heat transmission capabilities, alongside their effects on the crop health and sustainability of production.
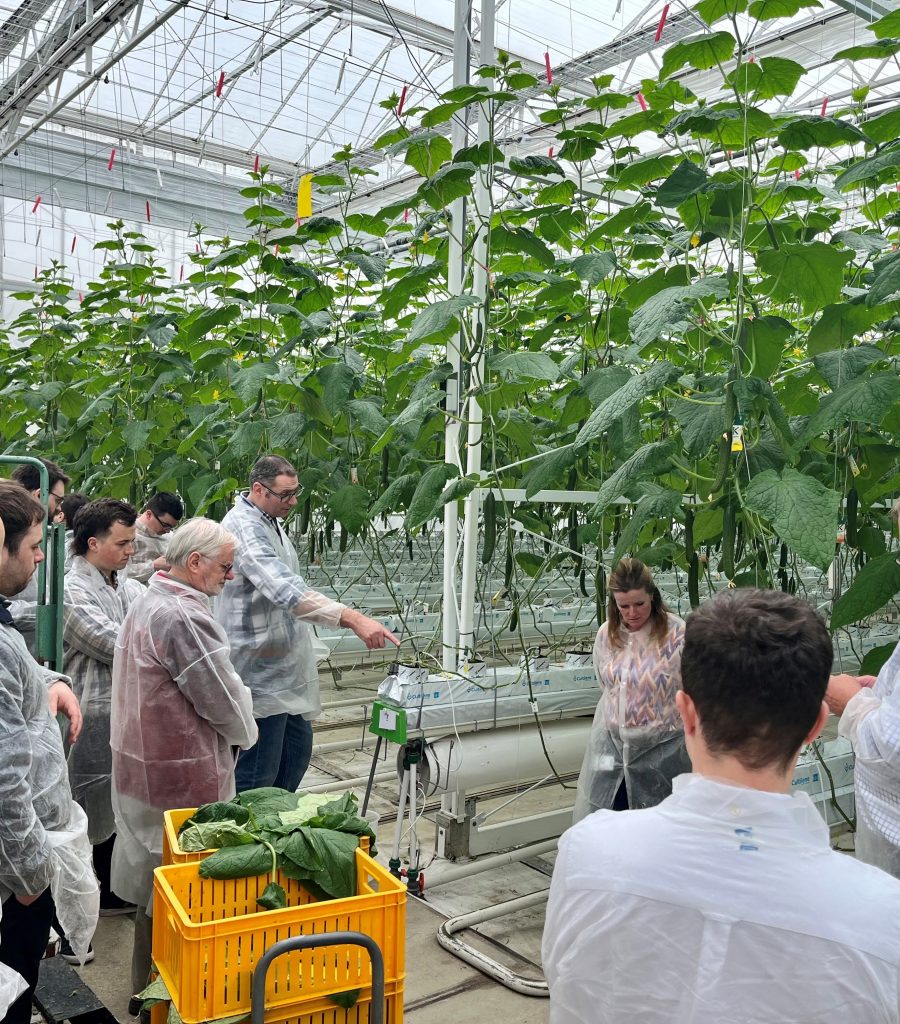
This article was written by Nathalie Key.
For active updates on the GrowSave project, visit our LinkedIn page or get in touch with Nathalie Key for more information.