Vertical farming emerged in a gradual way. Growers, experimenting with the opportunities presented by new technologies, added an upper layer of plants; this robbed the original layer of daylight, so lighting was provided beneath the upper layer; and the farm became vertical. Further layers were added. As progressively more artificial light was provided, with only the top layer (if any) enjoying daylight, side walls became insulated rather than glazed.
Vertical farming refers to the growing indoors, in stacked layers, of produce that would traditionally be grown outdoors, or indoors under glass. It offers higher growing density, and through use of emerging lighting technologies it reduces or eliminates reliance on natural daylight, which in any case in the UK is not always readily available. There are benefits to growing in re-purposed industrial buildings in urban areas, such as the opportunity to reduce food miles and to provide local employment; and of course, less land is required.
Vertical farming depends for its cost advantage on the likelihoods that in future carbon will cost more, and lighting from low-carbon electricity will become cheaper than fossil fuel heating. Previous Growsave Technical Updates have focused on improving energy efficiency in the traditional format; this update will examine whether the recent dramatic increases in the cost of energy are tipping the balance in favour of vertical farming.
All thanks to LEDs
The emerging lighting technology is of course LED, which over the past 10 years has become universal in general lighting, but which brings particular benefits to growing applications:
- LEDs can convert energy into light selectively, at desired wavelengths of the visible spectrum, tailored to produce the red and blue light necessary to stimulate plant growth without wasting energy producing green light that plants cannot absorb
- LED chips measure only a few millimetres, facilitating the production of infinite linear sources that may be positioned amongst plants, providing controlled uniform illuminance
- LEDs convert <50% of input energy into heat, much less than the fluorescent tubes used in early vertical farms; the requirement for cooling is lower, although not eliminated
Further advantages of LEDs are:
- Directional light output: no reliance on a reflector that can degrade
- Low operating voltage, safer in a humid environment
- Longer life with lower output degradation
- Glass free, eliminating the risk of lamp breakage, which can require complete decontamination
To put efficiency improvements into numerical context, consider that fluorescent tubes could produce 80-100 lumens/Watt, whereas white (broad spectrum) LEDs are reaching beyond 150 lumens/Watt with conversion efficiencies of over 50%. But the lumen is a unit intended to represent the response of the human eye; in horticulture, this ratio of light output to energy input is instead stated in mmol/J, where mmol (micromole) represents the quantity of photosynthetically reactive photons of light in the range 400-700nm, and J represents energy in Joules. A traditional HPS (High Pressure Sodium) light emits 0.9mmol/J, whereas an LED may achieve 2.7mmol/J.
Vertical versus traditional farming
A traditional heated glasshouse enjoys free daylight, but requires large amounts of heat, depending on the crop involved; cooling and dehumidification when necessary are achieved by opening roof vents. Heat is provided from gas or oil fired plant, usually a boiler but CHP is also popular. Recent improvements in these established technologies are marginal. The CO2 produced by combustion may be used to enrich the crop; some growers will also boost crop growth with artificial light, at further cost. This triple requirement explains the popularity of CHP.
By contrast, a vertical farm provides artificial light, and enjoys the “free” heat which any artificial light source generates (because not all input energy is converted into useful light). Depending on the lighting intensity and the building fabric, top-up heat may be required to maintain ambient temperatures suitable for growing, or heat from lighting may be excessive, requiring active removal to avoid overheating. Cooling the building may require refrigeration plant, and air circulation fans, which also use energy; alternatively, it may be possible to remove the heat at source using water-cooled LEDs, which in turn last longer. In either case, the recovered heat may be useful elsewhere on site. CO2 where required must be bought in, or generated in a fuel burner (providing unwanted heat), but low airchange rate makes concentration easier to achieve.
Energy intensities for conventional horticulture under glass are well established, and the principle that underpins vertical farming – that light is now cheap, but heat expensive – invites a numerical comparison.
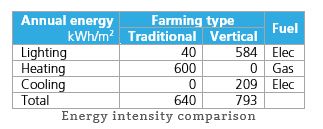
86% of the energy requirements of conventional farming are drawn from gas, which has a much lower unit cost than electricity. It might be expected that vertical farming, consuming over 2.5 times as much energy and all of it as electricity, would be prohibitively expensive to operate. Countering this are its lower land usage, the potential for LED growlighting efficiency to improve in future, the possibility of using free renewable energy and the predicted rise in taxation on carbon-intensive energy, which could reverse the relative costs of gas and electricity.